Crafting Your Own Surfboard: A Complete Guide
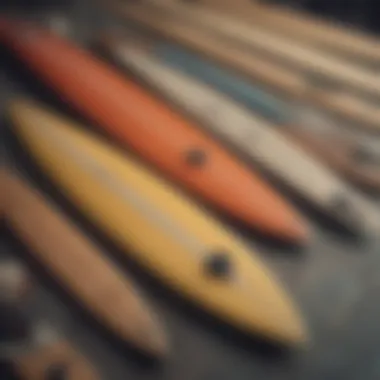
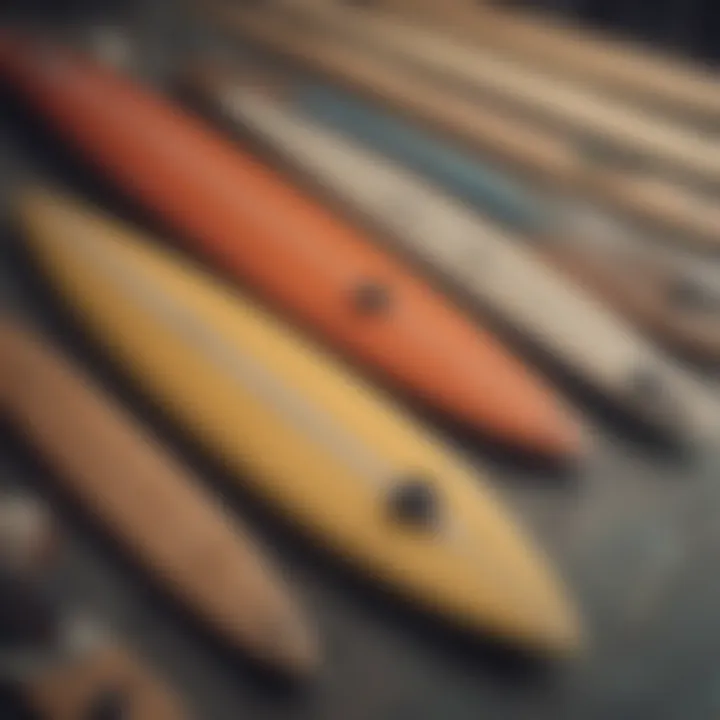
Intro
Crafting your own surfboard is a journey that goes beyond just the physical act of shaping foam and glass. It's about the connection you forge with the waves and the tool you create to dance across them. Every surfboard tells a story, from the design inspirations to the careful selection of materials. Whether you’re a novice looking at your first attempt or an experienced rider hoping to refine your skills, understanding the nuances of surfboard crafting can elevate your surfing experience.
This guide aims to provide you with clarity on the various facets involved in making a surfboard, ensuring you’re equipped with both the knowledge and confidence to embark on this creative endeavor. By unraveling the technical aspects and tying them to the art form, we hope to inspire you to step into the exciting world of surfboard making. This endeavor taps into the age-old fusion of creativity and functionality, where every cut and curve can drastically influence your ride.
As we dive in, we’ll explore the technology behind surfboards, the fundamental techniques every surfer should know, and a plethora of design insights that can make your handcrafted board truly unique.
Foreword to Surfboard Crafting
Crafting your own surfboard is more than just a hobby—it's a pathway to understanding the sport from its very core. For many, the thrill of catching waves is intertwined with the craftsmanship of their board. The importance of this topic lies in its ability to empower surfers, enabling them to create something that fits their unique style and preferences. This article takes you through the intricate process of surfboard crafting, covering everything from materials and tools to the artistry of design.
By diving into this subject, surf enthusiasts can unlock a world that enhances their riding experience. There's an unmistakable satisfaction that comes from paddling out on a board you've shaped with your own hands. This guide aims to highlight not only the technical aspects but also the personal touch that making a surfboard brings to the sport.
Understanding the Appeal of Custom Boards
When it comes to surfboards, finding the perfect fit can often feel like searching for a needle in a haystack. Off-the-shelf boards may meet basic needs, but they rarely cater to the rider's individual style, surf conditions, or even body type. Custom boards are the answer. They can be tailored in shape, size, and general characteristics to enhance performance. This personal touch can elevate a surfer's abilities and make the experience of riding waves that much richer.
Beyond performance benefits, crafting a custom surfboard brings an emotional connection between the surfer and their equipment. It's a union that fosters deeper respect and appreciation for both the sport and the craft. Many surfers find that building their own board turns into a meditative process—like a form of therapy where creativity and function intertwine. Indeed, the allure of custom boards is as much about performance as it is about personal expression.
Historical Context of Surfboard Manufacturing
Understanding the history of surfboard manufacturing is crucial in appreciating the evolution of this craft. Surfboards date back to ancient Polynesia, where they held cultural significance. Early boards were made from solid woods like the Ale or Koa, illustrating a deep connection to nature. Over time, the craft transformed through technological advancements, particularly after World War II, when lighter materials like foam began to replace heavy woods.
The introduction of fiberglass in the 1960s opened a whole new world for surfers, allowing for lighter, stronger, and more versatile boards. These developments sparked a golden age of innovation. Whether it was the introduction of shortboards during the revolution of the 1970s or the experimentation with various shapes and designs in modern times, each era changed the face of surfing. Today, blending traditional techniques with modern technology, the craft of surfboard making incorporates a myriad of materials and styles, showcasing the creativity and innovation of surf culture.
The history of surfboard manufacturing is not just about the boards themselves; it reflects the culture, innovation, and passion that surround the sport.
Crafting your own surfboard, therefore, allows you to tap into this rich history while creating something entirely unique. It draws from a long tradition of craftsmanship, inviting you to become part of an ongoing legacy.
Key Materials for Surfboard Construction
When embarking on the journey of crafting your own surfboard, understanding the materials involved is crucial. These materials not only give shape and structure to the board but also influence performance, durability, and the overall riding experience. Below, we’ll explore the key components that you’ll need to consider in your surfboard construction process.
Choosing the Right Foam Core
The foam core is the heart of the surfboard, providing the foundational structure and buoyancy that are essential for riding waves. Most commonly, shapers utilize expanded polystyrene (EPS) or extruded polystyrene (XPS) as the foam of choice. Each type has its unique characteristics. EPS is lightweight and often more forgiving in terms of shaping, whereas XPS offers superior water resistance and durability.
When making your selection, think about the conditions you'll be surfing in:
- Wave size and type: For larger and more powerful waves, a denser foam may be ideal to withstand the spills and tumbles.
- Weight considerations: If you’re keen on a lightweight board for maneuverability, EPS may be your best bet.
"Selecting the right foam can set the stage for your surfboard’s overall performance, like picking the right canvas for an artist."
Understanding Fiberglass and Resins
Once you have the foam core, you will need to bond it with a protective outer layer. This is where fiberglass and resins come into play. Fiberglass cloth is wrapped around the foam core and then infused with resin to create a tough outer shell.
There are two main types of resins used in surfboard construction: polyester resin and epoxy resin.
- Polyester resin is cost-effective and provides a solid finish, but it tends to be less durable over time.
- Epoxy resin, on the other hand, is stronger and provides better flex properties, making it suitable for a range of surfing conditions, particularly where impacts may occur.
Choosing the right combination of fiberglass and resin can significantly affect your surfboard's weight, strength, and flexibility.
Additional Materials for Customization
To make the board truly yours, you may also consider additional materials that enhance both function and aesthetics. This can include:
- Carbon fiber: Using this material can introduce lightweight strength and aid in performance, perfect for competitive surfers seeking an edge.
- Wood: Incorporating wooden stringers can enhance aesthetics and add natural feel to the board.
- Paints and graphical elements: Personalizing your board with designs not only makes it visually appealing but also creates an emotional connection to your craft.
When deciding on customization options, balance is key. Too many added features can weigh the board down. The ultimate goal is to complement performance while expressing personal style.
By thoughtfully selecting and integrating these materials, you can elevate your surfboarding experience and create a board that not only rides well but also resonates with your individual style.
Essential Tools for Surfboard Making
When embarking on the journey of surfboard crafting, having the right tools at your disposal is just as crucial as the materials themselves. Each tool is designed to serve a purpose and contributes significantly to the overall outcome of your board. Without the appropriate tools, any attempt at board shaping may lead to frustration and subpar results. It’s essential to invest time in understanding and organizing the tools needed to ensure your surfboard-making experience is efficient and enjoyable.
In this section, we will look at a variety of tools, both hand and power, that play a vital role in the surfboard making process, along with the necessary safety equipment to protect yourself during the process.
Hand Tools and Their Uses
Hand tools are often the backbone of surfboard shaping, providing a level of control that power tools might not always deliver. Here are some of the essential hand tools you’ll need:
- Surform Shaper: This tool works wonders for profiling and refining the shape of the foam. The Surform’s unique blade makes it easy to shave off excess material.
- Rasp and Files: These are indispensable for more detailed shaping and smoothing surfaces. They come in various coarseness, which allows a gradual refinement of your surfboard’s shape.
- Sandpaper: This is a must-have, with different grits available for initial shaping and finishing. Starting with a coarser grit and moving to a finer one results in a smooth finish without undesirable dips.
- Measuring Tape and Ruler: Precision is key in surfboard shaping. Accurate measurements ensure symmetry and performance, thus investing in a quality measuring tape is vital.
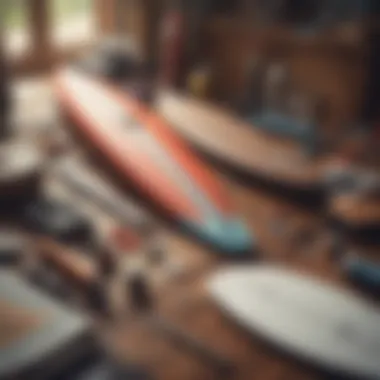

Each tool serves its own niche, and mastering their uses can put you on the path to crafting a quality board.
Power Tools for Precision Work
While hand tools are great for detailed work, power tools can make the job quicker and more efficient, especially for larger tasks. A few key power tools include:
- Electric Planer: This tool is essential for quickly taking off larger sections of foam. Its adjustable depth setting allows you to remove material without risk of gouging.
- Router: For adding fin boxes and other insets, a router is indispensable. It allows for clean, precise cuts that can be repeated consistently.
- Sander: A power sander significantly speeds up the sanding process. Whether you’re using a belt sander for general shaping or an orbital sander for finishing, this tool helps achieve that glassy surface finish on your board.
Using these tools permits you to work with higher precision than relying purely on hand tools, while also saving you time.
Safety Equipment and Precautions
Safety cannot be overstated when it comes to making surfboards. Working with foam, resin, and various tools poses inherent risks, so careful preparation and precautions are necessary:
- Dust Masks: Sanding or shaping materials generates a lot of dust. To avoid inhaling particles, wear a good-quality dust mask whenever sanding.
- Safety Glasses: Protect your eyes from foam debris and resin splashes. Frequent exposure to these elements can lead to irritations and long-term damage.
- Gloves: When working with epoxy and fiberglass, disposable nitrile gloves are essential to protect your skin from irritants.
- Ear Protection: Power tools can be noisy, and prolonged exposure can lead to hearing damage. Investing in earplugs or noise-canceling headphones can be a smart move.
By integrating these safety measures into your surfboard-making process, you can minimize risks and focus on creating your custom masterpiece.
Remember, the right tools paired with safety gear not only enhance the quality of your work but also protect you through the journey of surfboard crafting.
This section lays the groundwork for beginning your surfboard project, emphasizing the tools’ importance and ensuring you're well-prepared to shape your very own wave-riding vehicle.
The Surfboard Shaping Process
The shaping process is where the magic really happens in making your surfboard. It’s the step that transforms raw materials into a functional, performance-driven board. Here, craftsmanship meets functionality, and the choices you make can dramatically influence how your board rides the waves. Understanding this process is crucial for anyone looking to create a custom surfboard that fits their individual style and riding preferences.
Shaping your surfboard is not just about contouring the foam; it’s about creating a personal piece that resonates with your surfing ethos. In essence, it allows for an opportunity to integrate your vision with practical surfing demands, all while staying true to the art of surfboard crafting.
Creating a Template for Your Board
Creating a template is where your design vision starts to take form. You have to consider various aspects—length, width, and thickness. Drawing a template from existing boards or from outlines you’ve sketched will give you a physical representation of your idea. You might consider using cardboard or MDF to create something that is both light and easy to manipulate. The outline can be refined later, but the initial shape is key because it dictates both the aesthetics and function of the finished product.
- Find a board that you like: This could be your existing board or one you admire. Trace its outline onto your template material.
- Adjust the template: Consider what you want to improve or change based on your surfing style. Get rid of excess areas that may not serve your purpose.
- Finalizing the template: Ensure that the edges are smooth. This template will guide you during the shaping of the foam core.
Shaping the Foam Core
Once your template is ready, shaping the foam core is next. Using a hot wire cutter or a hand saw, this step allows you to outline and refine the shape of your board. During this process, it's vital to frequently check against your template to ensure accuracy, and nothing beats a keen eye for detail here.
As you carve away the foam, consider the rocker— the curve of the board from nose to tail. Too much rocker can hinder paddling, while too little can make your board hard to turn. Striking a balance is key. As you’re shaping, remember that the thickness distribution affects both buoyancy and overall performance.
Adding the Rails and Contours
Once the foam core is shaped, it’s time to focus on the edges. Adding rails and contours can be a transformative step for your board's performance. Rails refer to the edges which will come into contact with the water, and they play a crucial role in the board's maneuverability and stability.
Consider these points when shaping the rails:
- Round vs. Sharp Rails: Round edges are forgiving and better for beginners while sharper rails can give more response and control, preferred by seasoned surfers.
- Contouring the bottom: Whether you prefer a single concave or a more advanced multi-concave design will depend on your riding style. These factors will affect how water flows underneath the board.
So take your time here, as these elements contribute significantly to how your surfboard will perform on the waves.
"The surfboard isn’t just an object; it’s an extension of your being on the water."
Crafting your own surfboard isn't merely a hobby; it's a journey through creativity, physics, and personal expression. By understanding and mastering the shaping process, you are setting the foundation for a piece that reflects your surfing identity.
Applying Fiberglass and Epoxy
When it comes to surfboard construction, the application of fiberglass and epoxy is a crucial phase that directly influences the board’s durability and performance. This section will explore the importance of these materials, the intricate steps involved in their application, and critical considerations to keep in mind. By mastering this process, one can significantly enhance the longevity and overall effectiveness of their custom surfboard.
Preparing for Lamination
Before diving into lamination, preparation is key. First off, ensure your workspace is clean and free of dust, as any particles can lead to imperfections in your board. Additionally, gather all necessary materials: fiberglass cloth, epoxy resin, hardener, mixing containers, and brushes.
A good practice is to pre-cut the fiberglass cloth to the required size based on your board’s dimensions. This will save time and reduce the chances of mistakes during the application. It’s essential to mix the epoxy properly following the manufacturer’s guidelines; the right ratio of resin to hardener is critical for achieving the desired cure.
Tips for Preparation:
- Ventilation: Ensure adequate airflow to avoid inhaling fumes.
- Temperature: Work in a warm environment since epoxy cures faster in heat.
- Protective Gear: Always wear gloves and a mask to protect against chemicals.
Layering the Fiberglass
Now onto one of the more intricate parts: layering the fiberglass. The main objective here is to lay the fiberglass cloth over the foam core smoothly, allowing it to conform to the board's shape. Start by placing the cut cloth on your board and gently pressing down to eliminate any air bubbles. A common mistake is rushing this part; patience is crucial.
Once the fiberglass is positioned, use a brush to saturate it with the mixed epoxy. The key is to work from the center outwards, ensuring an even coverage. Aim for complete saturation without oversaturating, as excess can lead to a mess and increased curing time.
Layering Tips:
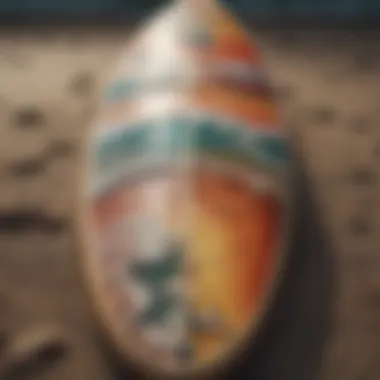
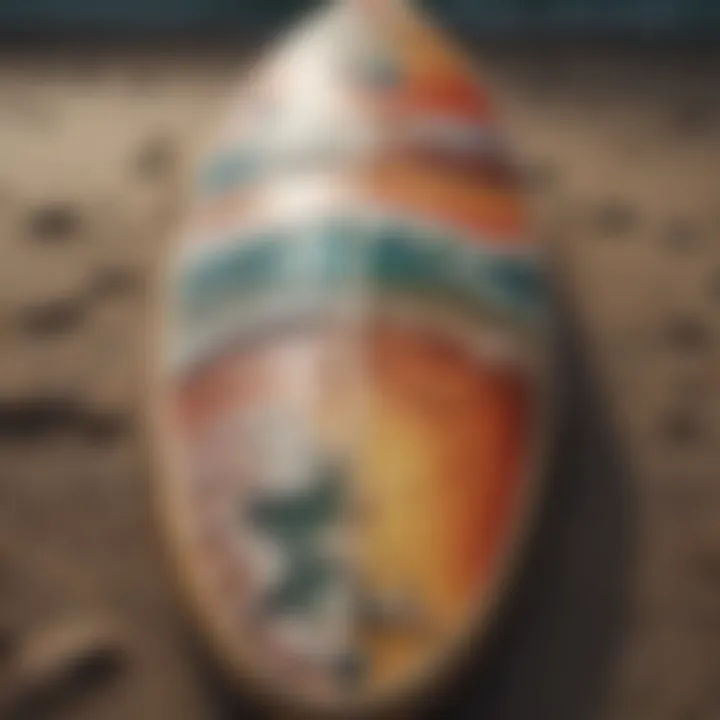
- Work Quickly: Epoxy can start to cure in about 60 minutes.
- Avoid Bubbles: Use a squeegee or brush to push air out gently.
- Multiple Layers: Depending on your design, adding multiple layers will enhance strength.
Curing Process and Temperature Control
After applying the fiberglass, the next crucial step is the curing process. This phase signifies the transformation of the wet resin into a solid, hard shell. It’s imperative to have an eye on the temperature as it significantly impacts curing time and strength. The epoxy needs a stable temperature range to cure correctly—typically between 70°F and 85°F is ideal.
Once laid, cover the board to prevent dust and debris from settling on it. The curing sheet should remain undisturbed. Full curing can take up to 24 hours, depending on the type of resin used and the ambient conditions.
Key Point: Lack of proper curing can lead to weak spots in the fiberglass, creating future issues while riding.
Curing Control Tips:
- Monitor Humidity: High humidity can affect curing; aim for a dry workspace.
- Check Progress: Periodically check for initial hardening, but avoid touching.
- Patience Pays Off: Resist the urge to rush into the next step until fully cured.
By mastering the fiberglass and epoxy application process, you are well on your way to crafting a surfboard that can withstand tumultuous waves while reflecting your personal style. This attention to detail is what can set your board apart—not just in aesthetics but in performance as well.
Finishing Touches on Your Surfboard
The finishing touches on your surfboard may seem like mere details, but they wield a significant impact on both aesthetics and performance. It’s the fine-tuning that elevates your creation from a simple piece of foam to a personalized masterpiece that mirrors your unique style and enhances your riding experience. From a sleek surface to visuals that pop, the finishing stage allows you to reflect your personality while also improving functionality.
Sanding Techniques for a Smooth Finish
Sanding is the key to achieving that ultra-smooth finish that not only looks great but also improves performance on the water. A rough surface can create drag, hindering your ability to glide smoothly. To start with, you typically want to begin sanding with a coarser grit sandpaper to remove any irregularities in the shape, especially around the seams where fiberglass and foam meet. Using something like 60 to 80 grit gives you a good foundation. Then gradually progress to finer grits—around 220 grit will give you that silky touch.
Here’s a quick run down of essential sanding steps:
- Start Rough: Use coarser grits to shape the board.
- Smooth It Out: Move to medium grit for an even surface.
- Finish Fine: Final touch with fine grit for a polished outcome.
Technique matters. Sand using circular motions and keep the sandpaper flat against the board to avoid dips or unevenness. Remember to vacuum or wipe down the board between grits to remove dust, which can cause scratches.
Applying Paint or Graphics
When it comes to aesthetics, paint and graphics tell your board's story. Applying a unique design can reflect your personality and create a distinctive look on the waves. To get started, select marine-grade paint or graphics designed for use on foam and fiberglass surfaces to ensure durability.
Before starting, make sure the surface is completely sanded and cleaned. You wouldn't want any dust or debris ruining your masterpiece! Using stencils can help create sharp lines and intricate designs. Remember to apply paint in layers—this approach helps to avoid runs and achieves that vibrant color that draws attention.
- Select Your Colors: Think about a color palette that resonates with you.
- Use Stencils: For complex designs, stencils will do the trick.
- Seal It: After painting, consider a clear marine varnish to protect your artwork and give it that glossy finish.
Installing Fins and Traction Pads
Fin placement is crucial to how your board performs in the water. Fins provide stability and control, enabling sharper turns and smoother rides. Make sure to install the fins according to the desired configuration—thruster, quad, or single fin setups each have their own characteristics.
To properly install the fins, measure out evenly spaced markings where you’ll place the fin boxes. Using a drill with care, make sure to create clean holes for the fin boxes.
After securing the fin boxes, it's time for traction pads. Traction pads not only provide grip but also add a touch of flair to the board. When picking a pad, opt for one with a good texture that fits your riding style. Installation is simple—align it at the tail end of the board, and make sure it’s securely adhered.
In summary, don’t skimp on the finishing touches. They define the look and performance of your surfboard. From sanding to artful painting and critical fin placements, each step matters significantly. Execute each with careful consideration and creativity, and you’ll have a board that’s as unique as your surf style.
Understanding Surfboard Design Elements
Crafting a surfboard is not just about assembling materials and tools; the design elements play a crucial role in how the board performs on the water. Understanding surfboard design encompasses the shapes, volume, and tail and nose variations—all of which influence your ride. Knowing these design aspects can greatly benefit both novice and seasoned surfers by helping them select or create a board that matches their surfing style and conditions.
Board Shapes and Their Impact on Performance
The shape of a surfboard directly affects how it interacts with the water. Different types of boards, like shortboards, longboards, and fish, have specific shapes designed for various performances. For instance, shortboards tend to be narrower, allowing for quick turns and agility—ideal for more advanced surfing maneuvers. In contrast, longboards generally have a rounded nose and a wider tail, providing more stability, making them suitable for beginners or for riding on smaller waves.
When it comes to surfboard shapes:
- Rocker: This refers to the curve of the board from nose to tail. Boards with more rocker are better suited for steeper waves, while less rocker is faster on flat waves.
- Width: A wider board will offer more stability, which is advantageous for beginner surfers, whereas a narrower design enhances speed and maneuverability.
Another notable shape is the Fish, featuring a unique design that combines width and a swallowtail. This shape not only adds buoyancy but also allows for impressive maneuvering even in less than ideal conditions.
Volume and Floatation Considerations
Volume is a key factor in how a surfboard floats in the water. A board with higher volume can support more weight and provides added buoyancy, which is essential for paddling efficiency and stability in the surf. For beginners, picking a board with sufficient volume helps in catching waves easier. However, as surfers progress, they may opt for lower volume boards for enhanced maneuverability.
When considering volume, keep these points in mind:
- General Guidelines: Generally, beginner surfers should look for a board that is wide and thick, while more experienced surfers might prioritize length and shape to enhance performance.
- Personal Weight: The surfer's weight plays a significant role in determining the volume needed. A heavier surfer will require more volume for optimal floatation compared to a lighter surfer.
Tail and Nose Variations
The tail and nose variations of a surfboard can completely alter the riding experience. A board's nose affects how well it penetrates the water, while the tail can impact the overall control and speed during maneuvers. For instance, a board with a pointed nose will slice through waves effectively, making it suitable for sharper turns and cutting into the face of a wave.
On the other hand, a square tail typically provides a good degree of stability with quick response—perfect for riding small or slower waves. Here are some common variations:
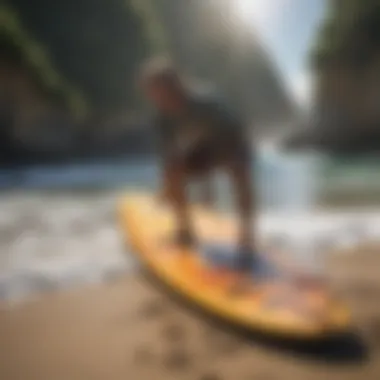
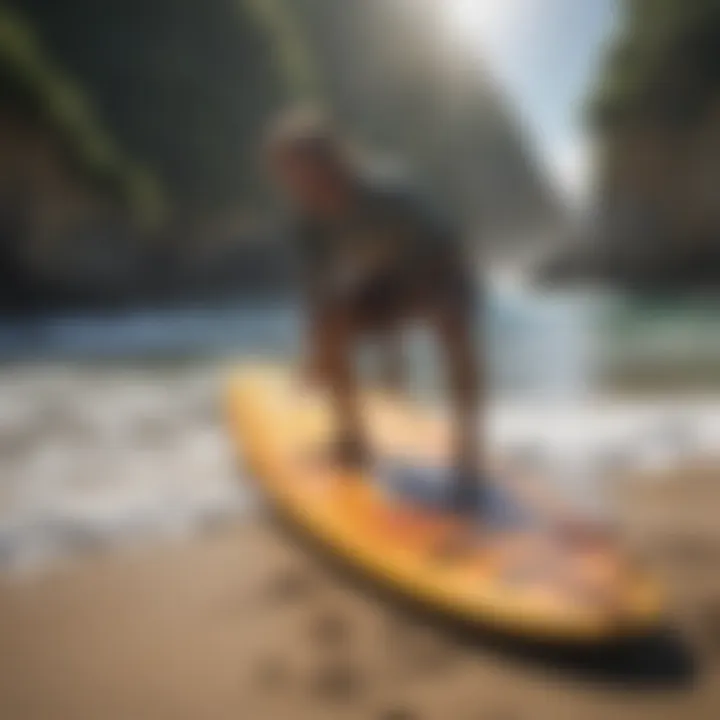
- Round Nose: Often found on longboards, ideal for noseriding and laid-back surfing styles.
- Swallow Tail: Increased maneuverability and speed, often preferred in performance shortboards.
- Pin Tail: Designed for critical turns and steep waves, offering a more controlled ride.
The specific design elements you choose can drastically enhance or inhibit your surfing experience. By understanding these factors, you equip yourself with the knowledge to select or design a surfboard that will suit your needs.
In short, investing time to learn about these design elements can make all the difference in shaping your surfboard to perfectly align with your surfing goals. Whether you’re just starting out or considering another custom project, taking these aspects into account is fundamental in crafting a board that sings on the waves.
Testing and Evaluating Your Surfboard
When you’ve invested time and effort into shaping and building your surfboard, the moment finally arrives to see how it performs on the waves. Testing and evaluating a surfboard goes beyond riding it for the thrill; it’s a critical part of the crafting journey. Assessing how your board reacts during a session can reveal adjustments needed to enhance performance. Whether you’re a novice or a seasoned surfer, understanding the way your custom board interacts with water waves can make all the difference.
Conducting Trial Runs
Trial runs are essential for anyone who wants to validate their craftsmanship. With each session, you will gather valuable feedback on performance. Start by selecting a day with waves that suit your expected board style. It’s best to avoid crowded waters—finding a quieter spot allows for focused testing, away from distractions or collisions. Here are a few key aspects to observe during your trial:
- Speed: How quickly does your board glide through the water? Does it feel sluggish or responsive?
- Turning Ability: Pay attention to how easily your board carves through the wave. A well-designed board should respond with minimal effort.
- Balance: Notice how stable you feel while riding. If you’re struggling to maintain balance, it might indicate the need for adjustments in volume or rail design.
- Comfort: Evaluate overall comfort—are your feet cramping or is your stance secure?
Take notes after each run with specific observations; this can help remind you what worked and what didn’t once you’re back in the shaping room.
Adjusting Based on Performance Feedback
After your trial runs, it’s time to analyze the feedback you’ve gathered. This post-evaluation stage can lead to meaningful modifications that elevate your surfing experience. Start by pinpointing any consistent issues you noticed during your rides. Perhaps you determined that your board is too stiff, or that it lacks maneuverability.
In making adjustments, consider:
- Shape Alterations: Fine-tuning the outline can vastly change performance. Slightly adjusting the tail or nose shape may enhance responsiveness.
- Rail Design: Think about experimenting with different rail shapes or sizes to improve your balance and ride.
- Fin Configuration: The type and placement of fins can significantly impact how your board reacts in the water—try tweaking angles or using different fin setups.
- Weight Distribution: If you found your board too heavy or unbalanced, redistributing foam or adding lighter materials could solve this.
"Fine-tuning your surfboard is like adjusting a musical instrument; even the smallest change can create a world of difference in performance."
Testing your surfboard isn’t just about finding what doesn’t work; it’s also about celebrating the success of what does. Each trial run not only affirms your efforts in craftsmanship but solidifies the bond you have with your board, making each ride not just a physical experience but also an artistic one. Persisting through evaluations and adjustments can transform that initial shape into a personalized masterpiece, landing you the perfect ride you envisioned from the beginning.
Maintenance of Your Custom Surfboard
Taking care of your custom surfboard is crucial for its longevity and performance. Whether you're a weekend warrior or ride the waves every other day, neglecting maintenance can lead to diminished performance and ultimately, the need for costly repairs. Thus, understanding the ins and outs of caring for your board is a worthy endeavor. It ensures your investment continues to bring you joy and serves its purpose on the water.
An essential aspect of board maintenance is keeping the surface clean and free from any debris or salt buildup. Not only does this help maintain the visual appeal, but it also protects the integrity of the materials, especially those delicate fiberglass layers. Moreover, periodic inspections can help you spot issues before they turn into significant problems, saving you both time and money in the long run.
"A well-maintained surfboard is like a loyal friend; take care of it, and it'll take care of you when you hit the waves."
Cleaning and Care Tips
Cleaning your surfboard might seem simple, but doing it right can make a significant difference. Start off by rinsing your board with fresh water after every surf session. This simple act removes salt, sand, and other organic material that can erode the board over time.
For a deeper clean, you can use a mild soap solution. Avoid harsh chemicals that could damage the shiny finish or the resin. Scrub the board gently using a soft cloth or sponge to avoid scratching the surface. Here’s a quick checklist for cleaning:
- Rinse with fresh water immediately after use.
- Use mild soap for deeper cleans.
- Employ soft cloths or sponges.
Don't forget about the wax; removing old wax periodically allows for better grip when you reapply. A proper waxing job not only enhances performance but also offers a layer of protection. When removing wax, try using a wax comb or your fingers for less hassle.
Repairing Dings and Scratches
Even the most careful surfers will face dings and scratches at some point. A scratch here and there is just part of the game, but ignoring these small blemishes can lead to greater issues down the line. Water can seep into the board, leading to delamination or more severe damages that require professional help. To avoid this, it’s essential to address any visible damage promptly.
For small dings, you can perform repairs at home using simple supplies. Epoxy resin kits are widely available and easy to use. Here’s a quick guide to assist:
- Clean the area around the ding with fresh water and let it dry completely.
- Sand around the damaged area gently to create a rough texture for the resin to adhere better.
- Mix the epoxy resin according to the instructions on the kit.
- Apply the mixed epoxy using a spatula or a small tool, filling the ding completely.
- Let it cure for the recommended time before sanding it flush with the board's surface.
- Optionally, respray the area to match the original color, if necessary.
When it comes to deeper damage, or if you’re uncertain about your skills, it might be best to seek professional help.
In summary, keeping your surfboard clean and repairing minor damages can prolong its life and enhance your surfing experience. Take pride in your custom board, and it will reward you for many seasons to come.
The End: The Art and Science of Surfboard Making
In wrapping up this exploration into the intricate world of surfboard crafting, it’s essential to underscore just how significant this journey truly is. Surfboard making is not merely about carving foam or applying fiberglass; it’s an expression of identity, a reflection of personal style, and a commitment to performance. Each completed board tells a story, combining artistry and scientific principles that govern how a surfboard interacts with water.
A well-constructed surfboard enhances the surfing experience, allowing enthusiasts to connect with the waves in profound and exciting ways. The right design not only influences how a surfer glides across the swell, but also impacts their ability to execute maneuvers. Thus, understanding the geometry behind shapes, widths, and fins isn't just a geeky pursuit—it's foundational for any surfer looking to elevate their game.
Reflecting on the Crafting Experience
Taking a moment to reflect on the crafting experience can bring about an awareness of just how valuable it is. Many who have taken to shaping their surfboard often recount that the satisfaction of riding a board they crafted themselves is unparalleled. It’s like riding a piece of their own soul, molded into a form that dances on water. This connection fosters a deeper appreciation for both the surfboard and the sport.
While engaged in this hands-on process, artisans learn about materials, ecosystems of the ocean, and performance attributes. Each strike of the tool against the foam resonates with insights on shape and balance. Surfers discover nuances in shaping techniques, learning how the slightest adjustments can alter the way a board performs. This transformative journey not only cultivates patience and technique but also reinforces the ethos of surfing culture as a deeply personal connection to the ocean.
Encouragement to Explore Customization
Customization opens up new horizons for any surfer willing to roll up their sleeves. There’s a world of possibilities just waiting to be explored. Why settle for factory-made, cookie-cutter boards? Creating a custom surfboard allows you to tailor every aspect—length, width, nose shape—based on personal surfing style and local conditions.
Benefits of Customization:
- Performance Optimization: Tailor your board to match your skill level, riding style and the surf conditions you typically face.
- Unique Aesthetics: Express your personality through designs that resonate with your identity. The graphics and colors you choose can represent not just who you are, but what inspires you.
- Enhanced Connection: As you invest time and energy into creating something unique, you nurture a bond not just with your board, but with the ocean as well.
In these final reflections, remember that surfboard crafting is much more than a hobby; it's a profound journey into the heart of surf culture. Using your hands to shape your ride is a celebration of creativity, passion, and personal connection to the waves. As you venture into this exciting arena, consider the immense satisfaction that comes from not just riding the waves, but from having created the very tool you ride upon.